- HOME>
- OUR BUSINESS>
- RESEARCH & DEVELOPMENT
RESEARCH & DEVELOPMENT
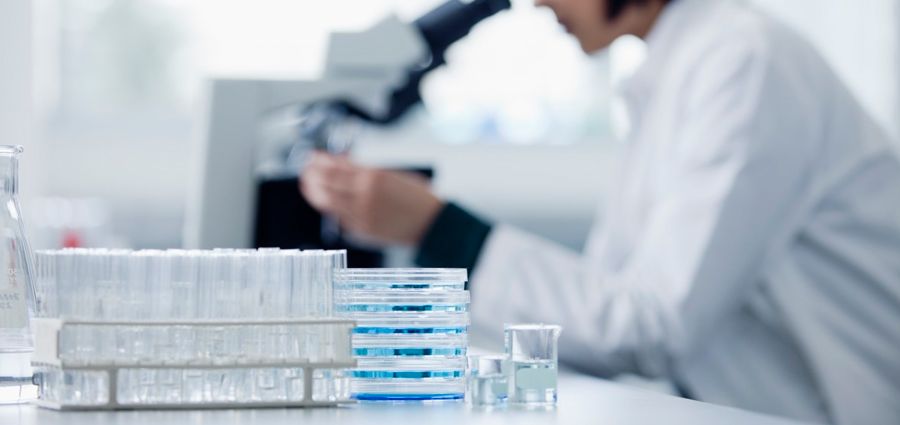
We devote continuously to study the leading-edge technologies and support in providing the advanced technologies and excellent services.
As a pioneer of manufacturers for water and wastewater treatment plant in Japan, our activities of research and development contribute to the advancement of technologies for various water and wastewater treatment.
Based on the reliable technologies developed over the years, we are providing the integrated solutions to meet the customers' concerns, together with more added value, and contribute to the sustainable development.
The role of research and development

In our research and development, we value the importance of always grasping the needs of our customers accurately and providing technologies that lead to solutions to their problems.
Our fields of Research & Development
The Research & Development Center has a large number of experienced staff.

We are carring out the research and development in all fields of water and wastewater treatment:
▸Technologies for water supply and sewage treatment
▸Technologies for sludge treatment
▸Technologies for manure and sludge disposal, recycle, and resue
▸Technologies for land leachate treatment
▸Technologies for various types of industrial water and wastewater treatment
Our mission
Our key strength is cross-cutting research and development in a wide range of business areas

It's the most important for our R & D to understand the needs of our customers accurately and provide the suitable technologies to meet these needs.
We believe that our key strength in research and development is our broad business scope that allows for cross-cutting research and development.
With the extensive knowledge and experience in water treatment that we have developed over many years, we are able to accurately and quickly respond to the various needs of our customers.

Furthermore, our R & D department has a large number of experienced staff. They always try to develop technologies not only with lab-scale experiments, but also with pilot scale studies and actual plants, which allow us to make various proposals covering all aspects up to O&M from the customer's point of view.
One of the key features of our solutions is that we start from customers’ needs, and could provide an one-stop service for water quality analysis, basic process design, EPC, O&M, and even chemicals.
Research and development achievements
Rephosmaster
-Phosphorus recover directly from the digestion solution discharged from the sewage treatment process-
1. We aim to solve our customers’ problems

“The treatment of digestion solution is labor intensive and costly in terms of maintenance of the dehydrator, pumps and piping. Are there any solutions to this?” This customer feedback led to the development of Rephosmaster.
Digestion solution contains high levels of phosphorus, which causes scale, in addition to various impurities. Scale caused by phosphorus is particularly difficult to deal with because it clogs pipes and equipments, such as dehydrators and pumps, where the digestion solution flows through.
On the other hand, phosphorus is a valuable resource that is going to deplete. It is reported that the phosporus in sewage accounts for up to 20% of the total amount of phosphorus that need to be imported in Japan. It's really important if phosphorus in sewage could be recovered and reused effectively, since the phosphorus in Japan relies entirely on the importation.
Thus, we decided to recover phosphorus directly from digestion solution to obtain phosphorus product that could be reuse directly.
2. A concrete example of our comprehensive strengths

It's easy to remove phosphorus from sewage, but difficult to recover from digestion solution as high-purity phosphorus product due to the influence of impurities.
For descaling in dehydrator, we provided various solutions with the cooperation between O&M department and chemical department, and accumulated many useful experiences and data in case studies for the development of new technologies. Furthermore, crystallization, the technology for solid-liquid separation in ore refinery plants and seldom used in water treatment, was adopted to develop the new technologies in R & D department, and then "Rephomaster" was developed successfully.
This technology was adopted by the Ministry of Land, Infrastructure, Transport and Tourism as a B-DASH (Breakthrough by Dynamic Approach in Sewage High Technology) project in 2012, and a two-year demonstration experiment named “Nutrient Removal and Resource (Phosphorus) Recovery, the Demonstration Project for Innovative Technology - KOBE Harvest Project in Kobe Higashinada Wastewater Treatment Plant" was carried out by a joint research entity comprising Kobe City, Mitsubishi Corporation Agri-Service, and Swing Corporation.
We are currently working for the wide application of this technology both in Japan and overseas.
3. Phosphorus Recovery Technologies from Digested Sludge
The relative high cost is the challenge for phosphorous recovery from sewage since phosphorus concentration in sewage is relative low.
Therefore, in order to reduce costs, the target for phosphorus recovery was shifted to the recycled water from anaerobic digestion solution with high phosphorus concentration. However, there is relative high concentration of solids in this recycled wastewater, which become the new obstacle and challenge for phosphorus recovery as high purity phosphorus product.
To address this technical issue, we developed a new phosphorus recovery process by incorporating a variety of our technologies, such as crystallization technology, which is already in practical use in the industrial wastewater treatment, and separation technologies used in mine refinery plants.
At the Rephosmaster demonstration plant, high-purity phosphorus product could be obtained from anaerobic digestion soulution with a solid concentration as high as 3%. Furthermore, the operating cost for recovery is only 1/20 of that in 30 years ago when it was developed.